dynaTWIN – Reducing Milling Vibration with Adaptive Spindle Speed Control
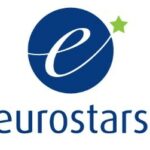
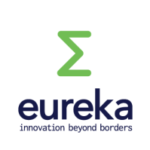
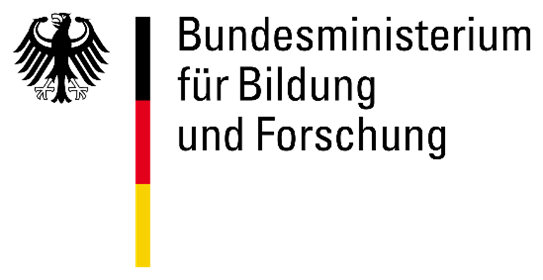
The research and development project “DynaTWIN” is funded by Eurostars (Eureka) and the Federal Ministery for Education and Research under the project no. E! 115498.
Details
Milling processes are highly dynamic. This is due to changes of stiffness and mass changes of the workpiece during the material removal, tool wear, deviations of the workpiece material batch, and tool micro geometry. These dynamics can lead to high local vibration amplitudes which limit the milling process and cause surface damages as well as decreased tool life and the consequence are higher costs for rework. With the use of three modules, the research project dynaTWIN aims to overcome these problems to enable high-productive milling processes of aero engine parts. The first module is about process stability and aims to allow a 5-axis dynamic and force simulation of complex shaped workpieces. The second module is the digital vibration twin module which can monitor and visualize the sensor and machine data of the toolpaths. The third module is the active vibration optimization module which adjusts the spindle speed according to the changing workpiece and machine dynamics.
High local vibration amplitudes can be the result of changes in the stiffness and mass change of the workpiece during material removal, increasing tool wear, deviations in the workpiece material batch and the tool micro geometry. Up to present time, there is no software that can simulate the dynamics and forces of complex shaped workpieces such as aero engines. The reason for that is that geometrical representation of the workpieces is used during the milling process, which cannot directly be used for FE simulation and need further processing. Also, data of the sensors and the machine is typically not processed via cloud-based frameworks, limiting the amount of processed data. Furthermore, current controllers do not adjust the spindle speed based on the changing workpiece and the machine dynamics.
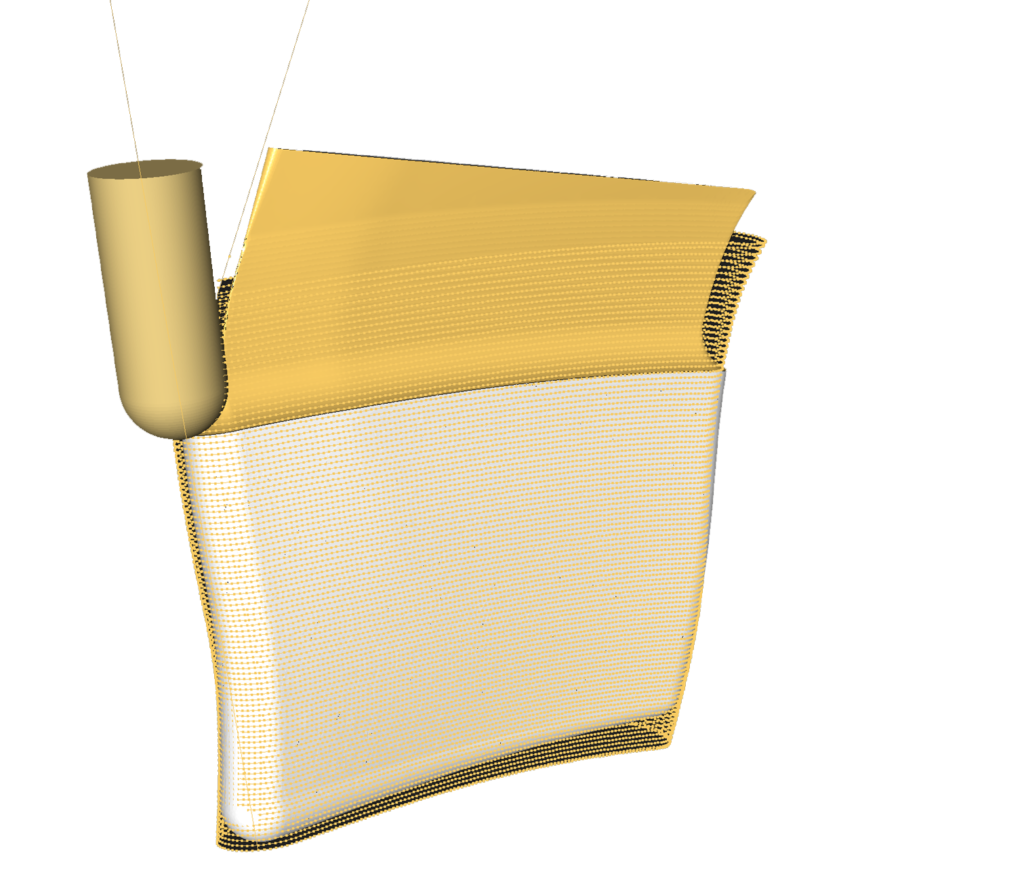
Visualization of milling an aero engine part.
The aim of the project dynaTWIN is to change this state of the art by developing three modules. The first module of the project will make it possible to simulate the milling forces, the changing workpiece and the machine tool dynamics in a simulation environment for 5-axis milling operations. To achieve this, the ModuleWorks CAM core will be implemented in Rhino to enable process planning for 5-axis milling processes and to simulate the geometrical workpiece-tool engagement. Based on the engagement simulation, a milling force simulation will be applied. The changing workpiece geometry during the milling processes will be gradually extracted on discrete cutter locations and processed for the usage in automatized modal simulations. These modal simulations will be transformed in a mathematical state-space representation which is beneficial for fast numerical processes.
For the second module sensor information, such as vibration or force and machine data, such as axis positions will be collected and automatically correlated to physical data like acceleration. This will allow to identify and analyze critical areas of the milling process. The collected data will be stored in a cloud and can be accessed from Rhino, a Webbrowser (Three.js) and will be visualized in virtual or augmented reality (VR/AR).
The third module deals with active vibration optimization. The position of the workpiece and the machine will be used for a model-based control and continuously updated depending on the current axis positions. This is done because dynamically changing process conditions like increasing tool wear, material damping, material and batch depending on cutting coefficients or the influence of process tooling. The approach for this module is to update the process model with real sensor data from the second module and provide a feedback loop.
The development of each module comes with a challenge. The first module is faced with the challenge of implementing different modules into one simulation framework and a user-friendly graphical user interface (GUI). The second module must overcome the difficulty of synchronizing and linking data from different sources as well developing a simple visualization control of the data in VR/AR which will work with most glasses. The third module involves adaptive spindle speed which requires the consideration of the inertia of the machine tool.
Once the challenges are overcome, it is expected that this framework will reduce vibration in the machining process up to 70% and milling times will reduce up to 50% in finishing processes. Surface quality may be improved up to 35%, while at the same time reducing tool wear up to 30% regarding mechanical wear mechanisms.
ModuleWorks is involved in the development of the dynamic simulation module, the development of the machine tool dynamics module and the visualization of vibration data.