Data-based Ramp-up Acceleration for resilient Manufacturing
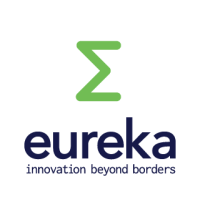
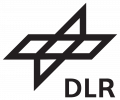
The project “DataRamp – Data-based Ramp-up Acceleration for resilient Manufacturing” is funded by the European Commission and the German Aerospace Center (DLR) under the project no.: E! 115645 / 01QE2140A.
Details
Tolerance violations during machining tend to waste time and materials in the production of metal parts and are caused by range of causes from tool or workpiece deflection to vibrations and tool runout. The aim of the project DataRamp is to develop a system for adaptive process planning, inspection and machining which enables efficient and reliable CAM programming and machining. This will be achieved by three loops that constitute the technology. A manufacturing loop will enable processing data on industrial practice. Secondly, an inspection loop will apply reverse engineering methods. Lastly, both loops allow the toolpath compensation of monitored errors, so that compensation based on data can be integrated in the CAM software.
The main motivation for the project are defects and tolerance violations due to tool or workpiece deflection, tool wear, vibrations and tool runout. Another issue is the fact that due to lack of evaluation tools, the generation of NC operations with tool parts and parameterization relies more on the experience of the process planner than on process data. Up until today, there is no cloud-based data storage, process and analysis application on the market that is dedicated to predictive quality. Also, inspections are only used to detect tolerance violations in a diagnostic manner that requires the manual intervention of the machine operator. No solution focuses on toolpath optimization in a prescriptive manner. These aspects result in the overall fact that no CAM software available on the market allows the compensation of a 5-axis toolpath that is based on manufacturing and inspection data.
Therefore, the project DataRamp, short for Data-based Ramp-up Acceleration for resilient Manufacturing, aims for a system that allows adaptive process planning, improved data-driven prescriptive inspection, and machining through manufacturing data. The technology will be achieved by three independent modules.
The first module is a manufacturing data-driven loop based on digital twinning which relies on data acquisition, processing, analytics and visualization of machine control and sensor signals to enable quality predictions. Inspection data will be based on tactile and optical measurement systems which are made available to the CAM kernel via a suitable reverse engineering method and a suitable interface framework. This should in turn make it possible to identify causal relationships between machining errors within CNC and profile deviation within CAQ. The main outcome of the project will be the toolpath compensation of monitored and inspected errors which are incorporated into the CAM software.
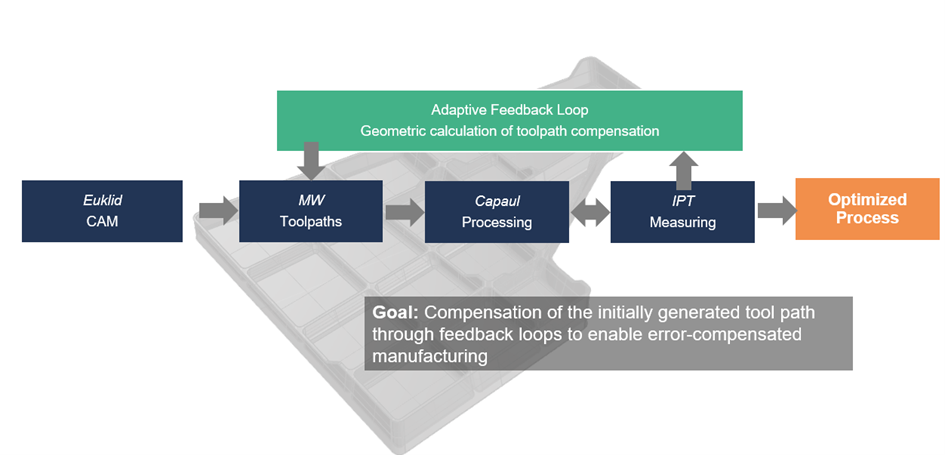
While the motivation to go beyond current industrial practices is an important step to improving manufacturing, it obviously comes with several challenges for the project and the respective modules. For the manufacturing loop, comprehensive data from different sources need to be acquired and subsequently transformed, synchronized, and linked.
This is done so that data of the machine control and additional external sensors can be assigned to their location on the workpiece surface. Additionally, the acquired data has a different sampling rate, so some of it needs to be sampled either down or up, and interpolation is also required. To minimize deviations, the accuracy of the measuring systems must be ensured in the single digit-micrometer range. To fulfill this requirement, a tactile coordinate measuring machine (CMM) and 3D measurement technologies are used. While tactile coordinate measuring has been a common practice for a long while, 3D measurement technology is relatively new and has not yet proven its usefulness.
Therefore, 3D measurement technology will be tested in specific use cases, while tactile coordinate measures will be used for benchmarking. With the development of the adaptive toolpath, it is important that small variations in tool design can result in considerable changes in engagement conditions. It is equally important to develop a time-efficient simulation framework to enable fast calculations. Equally important is the intuitive operation through the Graphical-User-Interface (GUI) for a high level of usability as well as a visualization of the simulated results is also part of the project.
Several improvements are tied to the project goals. For one, ram-up times and time-to-market will be reduced by 20% via the digital process chain, contour errors will be reduced by 30 to 50% through the process monitoring of critical process conditions, and quality assurance and certification times will be reduced by 50 to 70% by means of predictive quality while NC programming time is reduced by 50% on the data-based optimization of the toolpath. In short, the overall number of workpiece rejects will decrease while the number of first-time-right productions will be increased.
ModuleWorks’ role in the projects revolves around the development and integration of data sinks for the first two modules as well as the development of mathematical and geometrical algorithms for compensated tool path calculations. It also includes the development of a CAM module in Rhino 6 with the integration of the CAM Kernel into CAM software as well as the optimization of all developed modules.