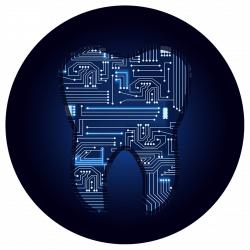
Simplified workflows
Improved quality and precision of dental indications
High-performance technology
Simplified workflows
Figure 1 shows how ModuleWorks Dental CAM (Dental Framework) combines additive and subtractive manufacturing, simulation, a toolset library and post processor in a universal dental CAM system that enables users to quickly select the best-suited and most cost-effective manufacturing process for each job.
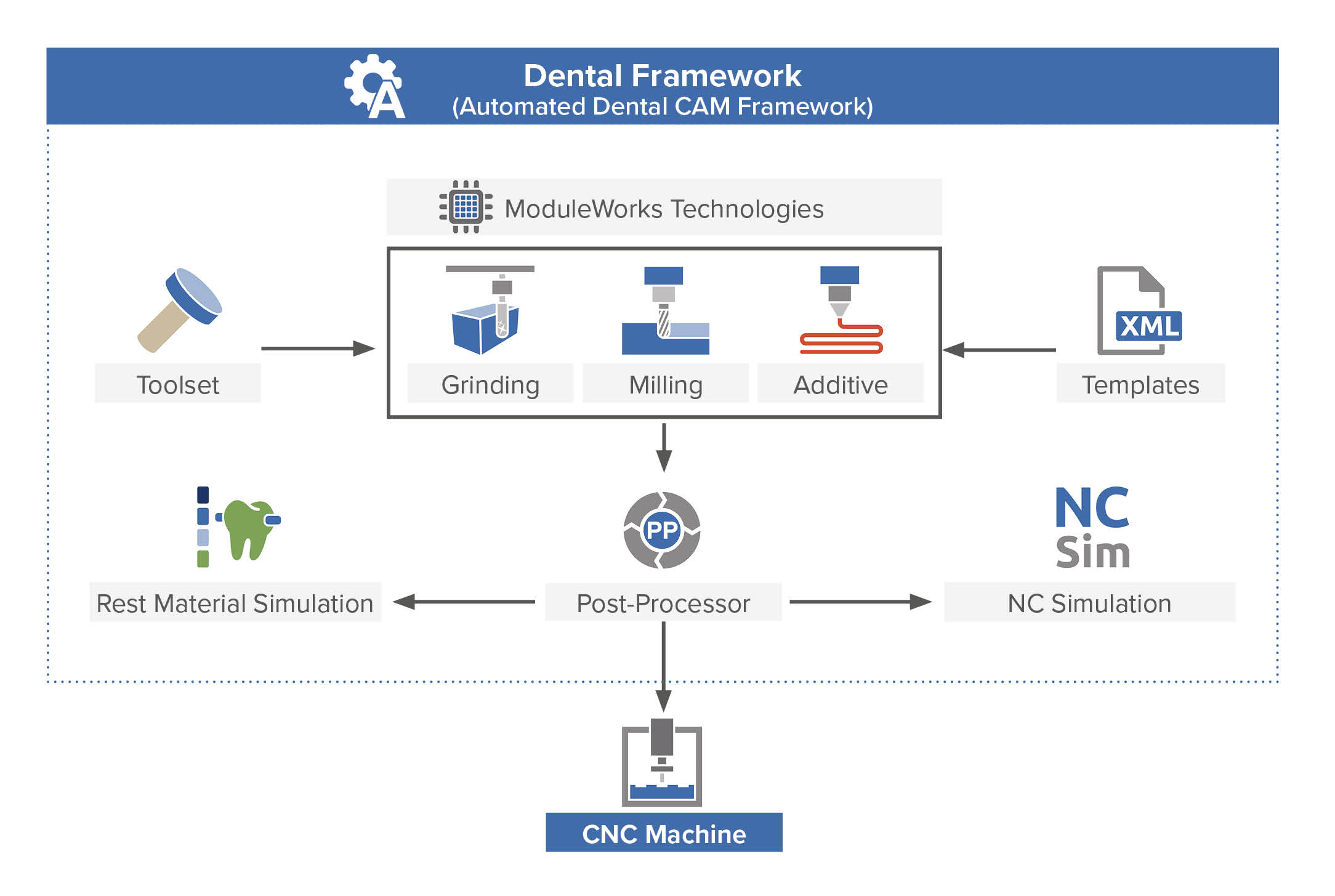
Improved quality and precision
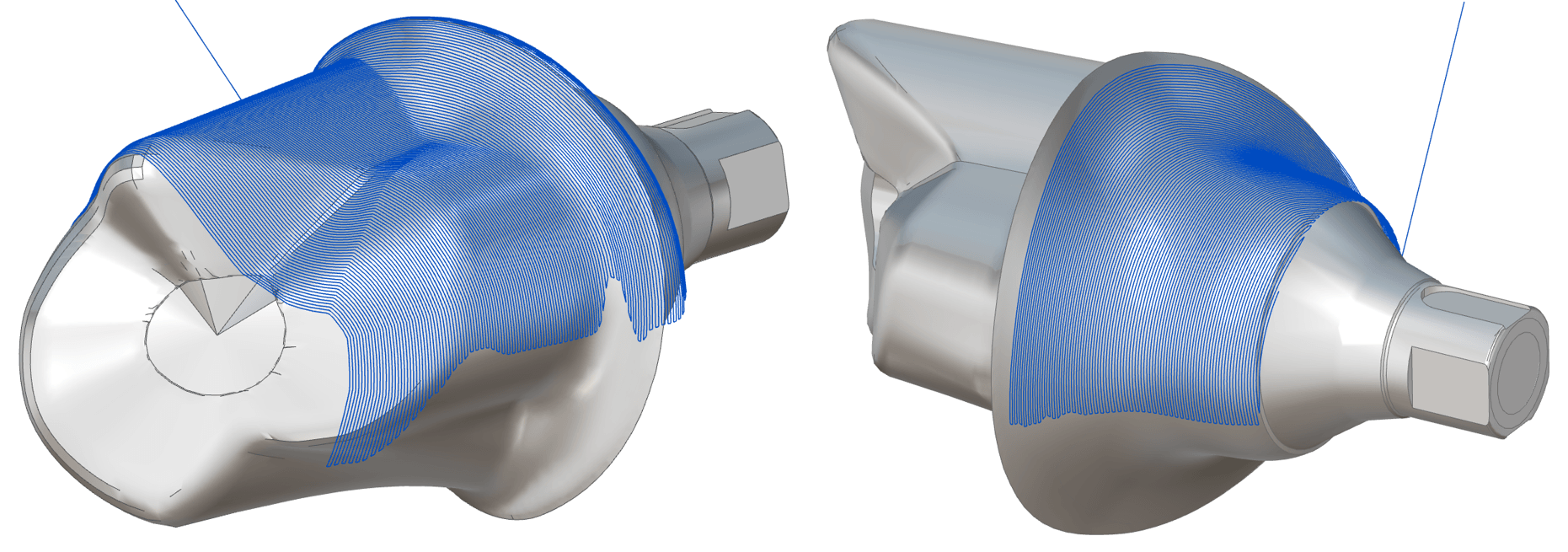
High-performance technology
A big cost factor is the time it takes to calculate the CAM toolpath. During the calculation, the workstation is occupied which means unproductive idle time while users wait for the calculation to finish. ModuleWorks Dental CAM takes full advantage of the latest multithreading techniques to speed up the calculation and keep production moving. Recent laboratory tests show that ModuleWorks multithreading on multi-core processors boosts performance by up to 75% in dental labs and up to 90% in chairside applications.
Average Performance Increase
over a single-core processor
Average Performance Increase
reduction in machining time
Summary: Right-first-time manufacturing
Visit ModuleWorks at IDS 2019 and LIGNA 2019
IDS 2019
Cologne, Germany
Hall 4.2, Booth M030 N031
IDS 2019
LIGNA 2019
Hanover, Germany