Funding agency: Bundesministerium für Wirtschaft und Klimaschutz / DLR Projektträger
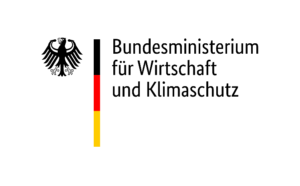
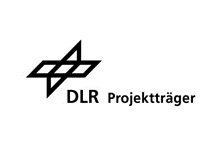
Details
High disposal costs and low material efficiency of maintenance and repair are still two factors that are getting in the way of sustainable aircraft production. To change this insufficient state, the project ORAM aims to recycle high-performance polymers for usage in the material cycle, requiring the establishment of a link between recycling and additive manufacturing.
High costs of disposal and low material efficiency of maintenance and repair processes are a stark contrast to resource scarcity and the need for sustainable air travel. ORAM aims to improve resource efficiency and reduce the emissions of the maintenance and repair of aircraft cabins by recycling and recirculating high-performance polymers.
This aim is reached by firstly testing a multilevel, selective recycling process for end-of-life airplane workpieces made of functional monomers, thereby getting a suitable recycled material for production processes. Through this, advantages of recycled materials for additive processes will be researched by successively mixing in new materials, further supported by digital manufacturing simulations. This will subsequently enable the parametrization of the printing process.
Alongside additive processes, alternatives such as thermoforming and injection moulding with recycled materials will be tested. The state-of-the-art so far has already shown that these processes require newly developed modules of additive production plants to process recycled materials into aircraft workpieces. With this knowledge an extended and intelligent extruder is being developed. This extruder will process filaments for applications for aircraft to equip additive manufacturing with recyclates and non-certified material groups. To meet the requirements for temperature resistant materials, these will be processed on a different demonstrator to get these products certified for aircraft.
The additively manufactured and researched products can be divided into three categories. The first category are jigs & fixtures. This includes the manufacture of jigs and other assembly aids for the superstructure, the transportation and repair of aircraft cabins from material blends (filament) with up to 50% secondary material by the end of the project. The second category are not-certified end-use-parts, which means that recycled materials are being researched for additive products of aircraft related applications.
The third category are certified end-use-parts. Here it is the aim to manufacture end products for the aircraft cabin. These material groups require a significantly higher processing temperature because authorization criteria such as low flammability have to be met. The focus of this part will be the galley or the lavatory so that material blends (maximum of 20%) can processed while the required characteristics of exemplary components of the aircraft cabin are fulfilled.
The newly developed recycling and additive production process will increase the usage of end-of-life-cycle parts of the aircraft cabin from currently 30 to 70%. The amount of crude oil to manufacture new components for the aircraft cabin will be lowered accordingly and thus allows a significant resource reduction.
Partners
Start: January 2023
End: December 2025