Funding agency: Bundesministerium für Bildung und Forschung / Projektträger Karlsruhe
Project Number: 01LY2203B
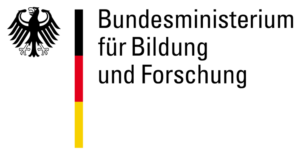
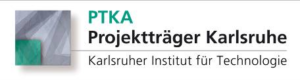
The project “MOBIDart” is funded by the Federal Ministry of Education and Research (BMBF) and the Projektträger Karlsruhe under the project no.: 01LY2203B.
Details
All levels of society are currently aiming to increase repair applications rather than replacing items, with the manufacturing industry being no exception to this. The repair of big parts or machine components is a huge commercial sector, but one that could become even more economically and environmentally attractive if cost and risk of transport for repair could be avoided. To make repair processes attractive, the project MOBIDart aims to combine laser metal deposition (LMD) and milling in a mobile repair tool. This mobile repair tool requires adequate software for the process management.
Numerous industries have large components that are essential for the functionality of product plants including energy technology and power plants, mining, wind power, (petro)chemicals and the automotive industry. The repair of these components is usually tied to a lengthy process of removing the damaged part and transporting it for repair as well as returning and mounting it after repair. This is tied to high CO2 emissions for transportation and economic costs due to downtime during repairing.
While mobile repair tools are currently already on the rise to improve the footprint and the prosperity of industrial production, the area and quantity of application is still comparatively low. This is why the project MOBIDart is setting up an innovative digital repair technology that combines LMD and milling. Apart from a reduction in CO2 emissions, MOBIDart strives to improve the already existing repair services of metalworking companies through the development of a resource efficient repair process.
So far, the maintenance of worn functional surfaces of large components has relied on manual applications of Tungsten inert gas build-up welding. This process is cumbersome as it requires several pre-processing and post-processing steps, geometric validations and the application of excess material which has to be removed later.
Laser welding is an alternative, highly automized process. It also has the advantage of allowing material deposition closer to the final contour which lowers time and cost intensive post-processing and the related resource consumption.
When using laser wielding close to final contours, the need for time and resources is lowered. More specifically, material savings can be tripled if LMD is used instead of Tungsten inert gas build-up welding. Furthermore, the abrasion of milling tools can be significantly reduced due to minimalization of the weld seam height, thereby increasing material efficiency not only in the workpiece, but also the tool.
ModuleWorks develops the software for the process control and makes sure the software is easy to handle and oriented on the industry’s needs and applications.
Partners
Start: January 2023
End: December 2025