Sustainable by Avoiding Residual Stress
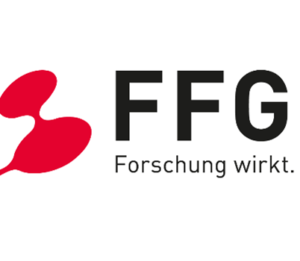
Details
Residual stress is a common kind of workpiece distortion caused by pre-machining operations such as forging, heat treatment, or cutting. These distortions have to be compensated which relies on experienced engineers and requires additional energy and by this causes CO2 emissions. Therefore, the project “AeroDOM” aims to develop an innovative simulation framework for aerospace-relevant bulky, forged Ti6-4 parts. The simulation framework will additionally be able to optimize machining strategies.
Residual stress is the phenomenon of post-machining workpiece distortion. Residual stresses can be induced by pre-machining operations such as forging or heat treatment and by the mechanical cutting process itself. Residual stresses cause various problems in industrial production as they lead to unwanted material distortions. The management of unwanted distortions is currently unstructured and done manually, based on the individual experiences of the engineers. Furthermore, process optimization is achieved through running several costly and time-intensive “trial and error” loops between the process engineers and the machine operators which require more electrical energy and create additional CO2 emissions.
Therefore, understanding the effect of partial material removal during machining on the residual stress redistribution is key for minimizing distortion in the final machining process. To overcome this, the aim of the project AeroDOM is to develop an innovative simulation framework, capable of numerically predicting part distortion behavior for aerospace relevant bulky, forged Ti6-4 parts. Based on this prediction, the simulation will be able to optimize the respective machining strategy. By that, costly, time-intensive, and unsustainable “trial and error” production loops can be reduced to a minimum, targeting the visionary approach of “first time right” machining.
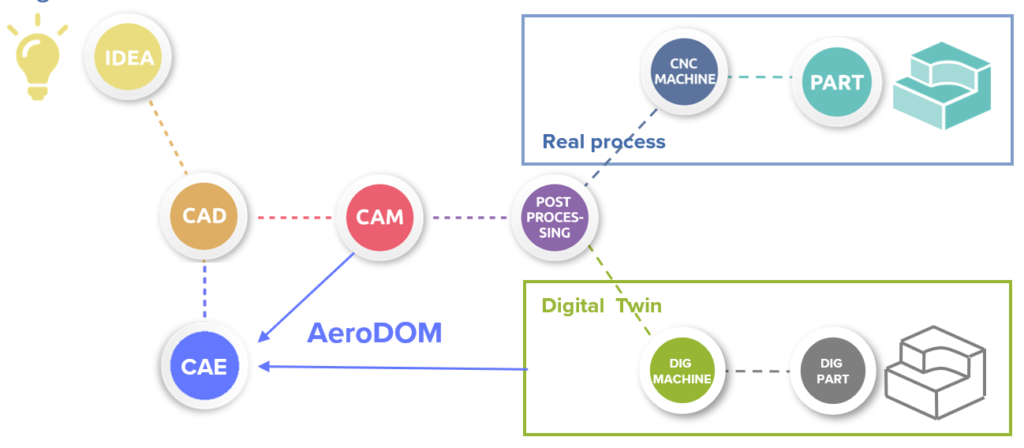
The project is innovative in several ways. Previously, most research has been focused on thin-walled aluminum workpieces. The distortion behavior of bulky, forged, Ti6-4 parts are now researched in the project for the first time. Secondly, the project develops a new residual stress model to simulate initial residual stress in the workpiece, instead of destructive measurements like previous models that only focus on the initial residual stress. Building on this new knowledge, the project will gather information on how to correct predicted distortions by influencing the machining strategy. Moreover, the project will develop a closed-loop with distortion optimization logic that unties finite element analysis data with dexel-based CAM material models.
The result of the project is beyond state-of-the-art research that focuses on industrial relevant Ti6-4 materials, develops a novel residual stress simulation model, and defines distortion optimizing machining strategies that are not yet available to science and industry.