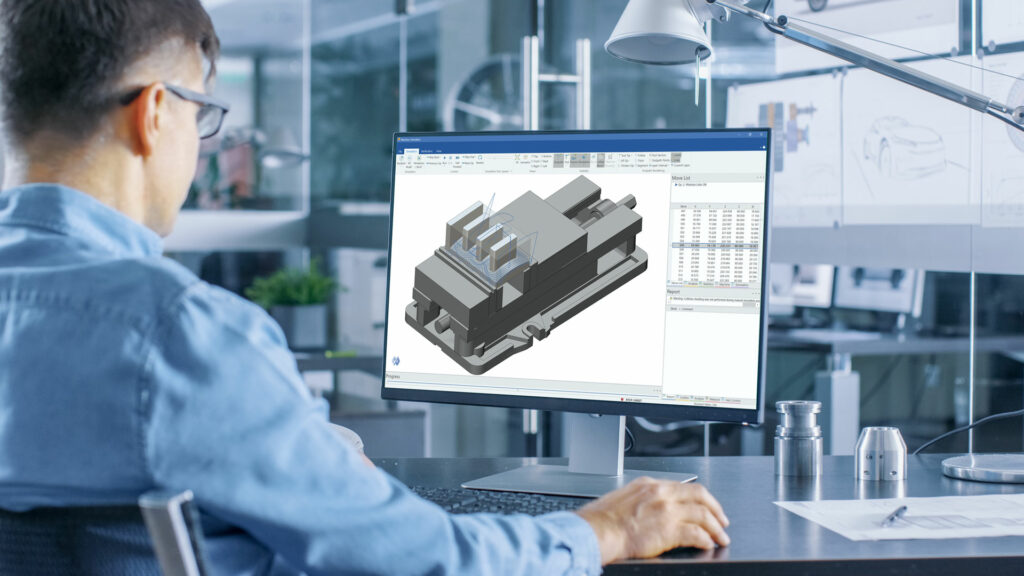
This release also includes additional features that improve the overall toolpath and simulation products offered by ModuleWorks.
Toolpath
Multi-Axis Roughing | Area Roughing
Avoid Small Profile Ramp
Challenge: With small profile ramps, users are limited to selecting tools with smaller non-cutting areas. Also, smaller ramps increase ramping time.
Solution: With this improvement, the minimum size of profile ramps can be controlled more accurately using an existing parameter.
Benefits: This improvement helps to avoid small profile ramps, thus allowing tools with wider non-cutting areas and improving tool engagement efficiency. Ramping time also decreases with larger ramps.
Multi-Axis Roughing | Area Roughing
Minimize Links
Challenge: In the multi-axis area roughing cycle, the start points in closed contours are currently positioned automatically based on the original offset contour’s start point. This can cause unnecessary ramps in many cases.
Solution: This new enhancement reduces the number of ramps in the multi-axis roughing strategy by optimizing the start points for closed contours. This means that some ramps are removed and, in these cases, the tool engages from previously cut passes.
Benefits: This reduces the total cycle time of the operation while increasing tool life.
Multi-Axis Roughing | Area Roughing
Trim Line Ramps
Challenge: For multi-axis area roughing, it is not currently possible to control the length of line ramps. Depending on the parameters, the length of the line ramp can be too long.
Solution: With this improvement, the line ramps are now trimmed to the stock.
Benefits: This improvement ensures that the ramp length is appropriately defined based on the available stock which, in turn, saves overall engagement time.
Multi-Axis Surface Finishing | Geodesic Machining
Improved Medial-Axis Cuts
Challenge: In a typical scenario, cusp heights in corners exceed the cusp height in areas of straight cuts. Unless the overall stepover is decreased, which increases the machining time, additional machining is necessary to achieve the desired surface specification.
Solution: This feature makes medial axis cuts more powerful. With this option, users can add additional medial axis cuts that are either merged with the main cuts or added as finishing cuts.
Benefits: This greatly improves the surface quality and reduces the manual effort to clean up the cusp afterwards.
Multi-Axis Surface Finishing | Wall, Floor and Rest Finishing
Stepover by Cusp Height
Challenge: Setting up the right stepover is a major impediment to achieving the desired surface finishing quality.
Solution: This enhancement adds an option to define the stepover based on the cusp height for advanced tools, such as barrel mills.
Benefits: With cusp-based stepover, users can quickly set up the operation and avoid mistakes from manual calculations.
Multi-Axis Surface Finishing | Wall, Floor and Rest Finishing
Tool Segment Selection for Tilting
Challenge: The geometry of advanced tools for five-axis machining, such as barrel tools, makes it challenging to generate an appealing toolpath and effective tilting motion.
Solution: A new feature enables users to define tool tilting using a segment of advanced tools such as barrel tools.
Benefits: With this feature, users gain greater control over the tilting range and the tool contact point for operations. This also improves user-friendliness and increases the surface quality.
Special Parts | Multiblade
Edge Rolling for Leading and Trailing Edges
Challenge: Each side of the blade may have different requirements for the edge, but currently the user is limited to the same setting for both edges.
Solution: With this enhancement, leading and trailing edges can now have their own edge rolling settings.
Benefits: This provides more flexibility to the users and allows them to define how the leading and trailing edges need to be machined individually.
Special Parts | Multiblade
Feed Rate for Leading/Trailing Edge
Challenge: The edge of blades can be very thin and some machines don’t cope well with fast kinematic moves while cutting material. If the tool needs to move from one side of the blade to the other at the cutting feed rate, the surface quality may suffer.
Solution: The leading and trailing edges can now have different feed rate sets allowing greater control over the toolpath.
Benefits: This helps to achieve better surface quality, with more consistent cutting and fewer abrupt machine tool moves.
Core Technologies | Linking
Fade Lead In/Out
Challenge: Currently, the lead-in and lead-out operations might leave cusps at the edges.
Solution: This feature adds a new lead type called “fade” for moving slowly towards and away from the machining surfaces.
Benefits: This produces better surface quality without any marks after tool changes, orientation changes, or machine downtime.
3-Axis Machining | 3-Axis
Optimal XY Angle for Flatland Milling
Challenge: When the part has multiple flat areas, users can only define a single XY angle which is not ideal for all areas.
Solution: The new enhancement now automatically detects the XY angle based on the longest section of the containment. This will ensure that the parallel passes are aligned with the longest edges.
Benefits: This improves the material removal and hence surface quality. Machining time is also reduced due to the optimized toolpath.
3-Axis Machining | 3-Axis
Ordering by Region
Challenge: Currently, parallel cuts toolpath ordering may leave a region unmachined in order to generate the shortest link to the next region. This might result in poor surface quality as the tool lifts and enters the same region multiple times.
Solution: The parallel cuts toolpath can now be generated using new region-based ordering. Each region is milled completely and then the tool moves to the next region.
Benefits: This provides better surface quality as there are no engage or retract moves in one region.
3-Axis Machining | 3-Axis
Outside-In Ordering for Flatland Milling
Challenge: Currently, for flat areas with multiple islands, the toolpath starts in the middle of the flat area and moves out to the flat boundary. This engages the tool vertically on the surface which reduces tool life, increases tool load, and can leave marks on the surface.
Solution: The ordering of the flatland toolpath has been improved and now the passes are ordered from the outside to the inside of the island or region.
Benefits: This would help to improve the surface quality and greatly increase the tool life since the tool will no longer engage directly on the surface from the top.
Turning | Turning
Adaptive Cut Pattern for Grooving
Challenge: Currently, it is difficult to machine deep cavity grooves.
Solution: The adaptive cutting pattern is now supported for grooving operations.
Benefits: The new adaptive cutting pattern makes it easier to machine deep cavity grooves. The adaptive pattern also improves tool life and reduces cutting load.
Turning | Turning
Roughing on Face Side
Challenge: Previously, it was only possible to generate a roughing toolpath for turning processes on the outer and inner diameters of the part. For face roughing, it is favorable to use a roughing operation instead of a grooving operation.
Solution: This new enhancement allows users to generate a roughing toolpath on the face side of the job.
Benefits: Using this strategy, it is now possible to effectively perform roughing on the face side of the job.
3-Axis Machining | 3-Axis
Store Contact Point Normals
Challenge: Currently, 3D cutter compensation is not possible for finishing toolpaths due to missing contact normal information.
Solution: This new enhancement for 3-axis finishing toolpaths stores the contact point normals along with the toolpath in the structure.
Benefits: These contact point normals can be used subsequently for 3D cutter compensation or tilting in the 3-axis finishing strategy.
Simulation
Simulation Systems | NC Editor
Axis Mapping
Simulation Systems | NC Editor
Open Active Machine in Machine Builder
Simulation Systems | NC Editor
Save Favorite Machine
Challenge: Currently, users have to scroll through the machine library list every time, even though the same machine is selected in each case.
Solution: A new feature marks the most-used machine as the favorite.
Benefits: With this feature, users can find the most used machine on top of the list thus reducing the time to find the required machine from the machine library list.