Direct Energy Deposition
Powerful and Advanced Manufacturing Solution for Direct Energy Deposition (DED)
The ModuleWorks Direct Energy Deposition (DED) solution is tailored for organizations offering CAM software solutions for powder welding components used with machine tools or robots. This includes CAD/CAM software developers looking to break into the additive manufacturing market, as well as robot integrators, robot OEMs, machine tool builders, and welding hardware manufacturers who develop solutions for this process. With ModuleWorks DED, these companies rapidly develop innovative and powerful DED solutions and features and get them to market fast. Typical DED applications include repairing and rebuilding the worn surfaces of pre-machined metal forms, such as metal forming dies for car body sheets. ModuleWorks DED also supports the EHLA technology.
Major Challenges
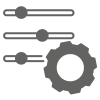
Optimization of Parameters
DED is a complex and sophisticated manufacturing process requiring accurate control over various deposition parameters such as feed rate and laser power to ensure a stable result and near net shape structure.
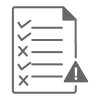
Reducing Defects
DED is also prone to a number of defects such as porosity and distortion of the laser spot. Controlling the repeated cooling cycles during layer-by-layer deposition is vital for high quality results. Consistent nozzle orientation is also crucial for keeping the surface perpendicular, thereby minimizing distortion.
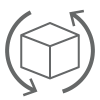
Post-Processing the Part
Parts manufactured using the DED process often require post-processing to achieve the final surface quality and required precision. This includes additional machining to finish the surface with the desired dimensions while staying within tolerances.
Solution Offered by ModuleWorks
ModuleWorks Direct Energy Deposition (DED) is an advanced and proven solution optimized for multi-axis, multi-layer additive manufacturing processes. It comes with an integrated toolpath planning algorithm specially designed for complex geometries and customized structures. Precise control and adjustment of process-critical parameters enable specific wall widths and heights (multi-layer) with maximum deposition efficiency, resulting in near net shape parts that require only minimal post-processing.
Key Features
Select the optimal toolpath pattern based on your part geometry or specific requirements. ModuleWorks offers a morph toolpath pattern that automatically adapts to the contours, creating continuous and efficient toolpaths. The morph pattern offers a full range of toolpath options and settings. It is also possible to generate parallel or spiral patterns.
Key Highlights
Advanced Toolpath Generation for Complex Geometries
The solution is based on freeform slicing and supports up to 6-axis toolpath calculations. The pattern is driven from a base curve, or a drive mesh surface, and all weld slices are created as 3D-equidistant paths from that contour. Various options allow precise control over the toolpath. Additional options like support for constant distance between the welding slices, lead/lag angles or side tilt angles, full collision avoidance and multi-layer welding toolpaths ensure optimum toolpath generation. Precise control over the direction and movement of the nozzle ensures the optimum angle for each manufacturing process, resulting in a consistent melt pool.
Hybrid Manufacturing
Easily switch between additive and subtractive manufacturing processes to rapidly build finished parts and implement closed-loop processes. The industry-proven, best-in-class subtractive manufacturing toolpaths from ModuleWorks integrate seamlessly with the DED technology for end-to-end hybrid manufacturing of high-quality finished parts. The solution is ideal for hybrid machine tools, robotic systems, and powder nozzle additive manufacturing. Fast and intuitive programming of 5-axis simultaneous toolpaths and full simulation of both DED and milling processes deliver optimum manufacturing flexibility and safety.
Key Benefits

Industry-proven DED solution for precision manufacturing of even the most complex parts

Reduced development and maintenance costs and rapid implementation for being first-to-market with the most advanced features and functionalities such as multi-body, constant distance, and angle orientation

Opportunities for collaborating on joint development projects with ModuleWorks to form a mature technological landscape for DED

Manufacturers utilizing DED benefit from increased productivity and flexibility through regular software upgrades to the latest available technologies

Repair and add features to existing parts and tooling. This reduces overall investment and is more sustainable than building new parts
Customer Success Story
ModuleWorks Unleashes the Full Potential of InssTek DMT® Technology

InssTek Inc. has integrated the ModuleWorks additive manufacturing calculation core into its DMT® (Direct Metal Tooling) technology. The innovative ModuleWorks software enables InssTek to use the multi-axis traversing capabilities of its DMT® machines to provide a fully automated, cost-effective solution for simultaneous 5-axis additive manufacturing and repairing of complex parts.